Sollten Sie mit Fertigungsrobotern arbeitet, ist RoboLive® Ihnen sehr wahrscheinlich bereits geläufig. Schließlich arbeiten mittlerweile weltweit Hersteller und Systemintegratoren, Werksleiter und Roboterprogrammierer damit, um Roboterprogramme effizienter in Betrieb zu nehmen oder während des Betriebs tiefergehend zu analysieren. Und das ist kein Zufall, immerhin wurde RoboLive® ursprünglich für den eigenen Bedarf auf der Grundlage jahrelanger Erfahrung in der Fertigungsautomatisierung entwickelt.
Es waren Ingenieure der Dressler Automation, die primär ihre eigene Roboterprogrammierung optimieren bzw. kontrollieren wollten. Wer hätte ahnen können, dass sie damit den Grundstein für die neuste Entwicklungsstufe eines seit jeher agilen Unternehmens legten?
Gegründet wurde die Dressler Automation 1970 in der Nähe von Braunschweig . Das Ingenieurbüro begann lediglich mit zwei Personen, die in einem kleinen Büro die Elektronik planten und im Garagenhof die Schaltschränke händisch zusammenbauten. Das Unternehmen wuchs schnell. In den 80er Jahren spezialisierte sich die Dressler Automation als eines der ersten Unternehmen auf die Programmierung der ersten Steuerungen. Und mit den Projekten wuchs das Unternehmen, die Dressler Automation entwickelte sich zu einer weltweit führenden Größe der Automatisierungstechnik. Mit der aufstrebenden Robotik folgte früh die weltweite Online- sowie die Offline-Inbetriebnahme von Fertigungsrobotern. 2010 eröffnete man die erste US-Niederlassung in Chattanooga, Tennessee, einer damals aufstrebenden Region Zentrum der Automobilherstellung.
Seit jeher erfand die Dressler Automation sich neu und gestaltete dabei die Welt die Automatisierungstechnik wesentlich mit. Und so kam es zu RoboLive®.

Jede Medaille hat zwei Seiten, und so ist auch die Industrie 4.0 Fluch und Segen zugleich. Denn während Zyklen kürzen wurden und der Druck der Inbetriebnahme stieg, erschwerten die steigenden Mengen an Prozessdaten zunehmend die Handhabung von Fertigungsrobotern. Um die eigene Effizienz zu steigern, begann man Ende der 2010er Jahre, eine Antwort auf zentrale Fragen zu entwickeln. Wie können die Unmengen an Roboterdaten sinnvoll genutzt werden, um simulierte Roboterprogramme sicher in der Realität umzusetzen? Wie können Roboterprogrammierer sicherstellen, dass die Inbetriebnahme korrekt erfolgt ist? Wie können alle Mitarbeitende sämtliche aktuelle Prozessparameter – egal ob Schweißen, Kleben oder Clinchen – auf einem Blick wahrnehmen und so Fehler vermeiden? Wie können Veränderungen nachvollzogen werden?
Heute stellt all dies dank RoboLive® längst keine Herausforderungen mehr dar. Denn mittlerweile ist auch RoboLive® gewachsen und beinhaltet diverse Funktionalitäten wie beispielsweise die Kalibrierung von Roboterprogrammen, die Korrektur fehlerhafter Koordinatensysteme und die automatische Erstellung von Dokumentationen. Der Kern der Lösung ist dabei die Visualisierung von Prozessen, die in regelmäßigen Abständen automatisch sämtliche Prozessdaten aller Roboter abruft, sie mit Soll-Daten abgleicht und an einem 3D-Modell des Produkts visualisiert. Dabei werden Code Rules, Roboterkinematiken und spezifische Standards berücksichtigt, sodass sämtliche Abweichungen vom Soll sofort erkennbar sind.
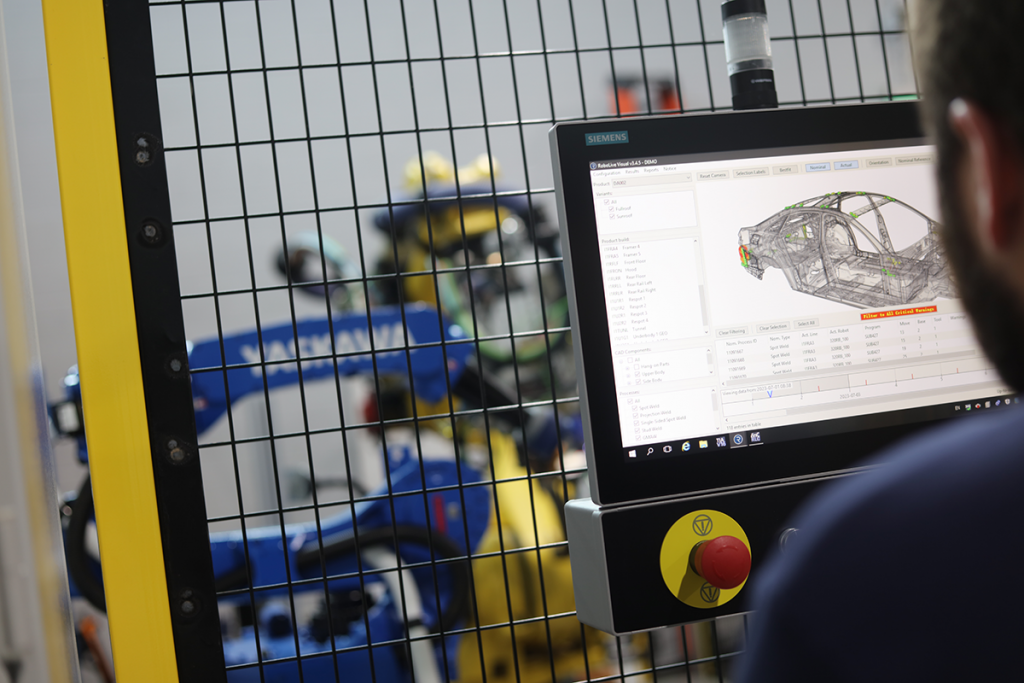
Was zunächst lediglich ein kleines Pilotprojekt an den Fertigungslinien in Chattanooga war, wurde schnell dank der enormen Reduzierung von Stillstandszeiten und Ausschuss zu einem werkweiten – und mittlerweile weltweiten – Erfolg. Dank des positiven Einflusses auf die OEE und der Einfachheit bei sowohl Implementierung wie Benutzung entwickelte RoboLive sich rasch weiterentwickeln. So wird es heute nicht nur bei der automatisierten Fertigung von PKW, sondern auch von Batteriegehäusen und LCV verwendet.
Für welche Herausforderungen mit roboterseitigen Produktionsdaten auch immer – es lassen sich immer individuelle Lösungen basierend auf einem erprobten System finden.